In my other life, as the printer at the Cumberland Village Heritage Museum in Ottawa, I get to demonstrate some beautiful vintage printing equipment to our visitors. Most of the time, I work on our trusty Chandler and Price New Style (14 x 22) — and sometimes we ink up one of the small table-top presses to let our visitors print their own little souvenirs. It’s an opportunity to share something of printing history and my joy in the craft. It’s a pretty cool job.
The Mysterious Whitlock
But standing silently in the background of the shop for the past 35 years is the enigmatic Whitlock Two-Revolution Cylinder Pony Press. Moved into the museum c1992, the press has mystified us for years. Other than a faded plate indicating that the press was sold from Montreal’s George M. Stewart Printing Machinery Co., we have very little information about its provenance. From the tympan and packing papers, we know that its last job was in 1989 (!), printing paint-can labels for a now-defunct paint manufacturer.
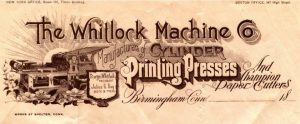
The Whitlock Manufacturing Company built cylinder presses in Connecticut between 1880 and 1918, with variations of the four-roller Premier Press and the smaller, two-roller Pony press. By 1918, Whitlock merged its operations with United and Potter Printing Companies to become the Potter-Premier Printing Company. Like the Babcock and Cottrell two-revolution presses, the Whitlock was a well-known workhorse for printing companies throughout North America. When surveying editions of Canadian Printer, Inland Printer and several other periodicals, I found that the Whitlock was regularly advertised, endorsed and sold throughout our country and the US. As best as I can determine, our pony press was manufactured between 1910 and 1913.
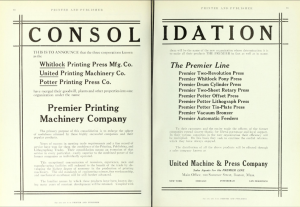
To our knowledge,* the only other working Whitlock Press in North America is located at the Marshfield Heritage Festival in Wainfleet, Ontario. Operated by the volunteers at the Mackenzie Printery, near Niagara-on-the-Lake, the Whitlock operates once per year, on Labour Day Weekend, much to the delight of the festival’s visitors.
An exciting challenge
This year, our managers challenged us to get our behemoth up and running. They secured a budget and we have an enthusiastic staff. Our team, comprised of Clay MacWhirter (a talented young member of the team with a degree in mechanical engineering and a knack for restoring vintage machines), Alex Wilkinson-Cruddas (a smart young historian and energetic apprentice printer), Bill Ellis and myself (both keen letterpress printers), was eager to get to work.
But while we understood the principle of how the two-revolution cylinder works, none of us had any actual experience or expertise on this kind of press. We needed an operating manual. I thoroughly scoured libraries, archives, museum and the internet. We pestered other printing aficionados, posted on several letterpress websites and listservs. We visited the library of the Canada Science and Technology Museum. But could we find a copy of a manual? A parts list? Nope. Nothing.
The lack of documentation is one reason why I decided to write this post. I’ve also posted a selection of videos on my Youtube channel, here. The other reason I’m posting this is simply to relate the sheer fun of working on this project.
Where to start?
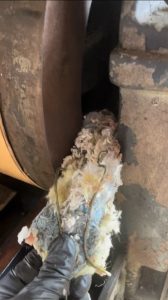
Work began in earnest in April 2024, before the museum opened to visitors. After 35 years standing in an unheated heritage building, we feared the worst: rusted or seized up gears, missing parts, metal fatigue or cracks. Clay started by removing the old power source, some kind of weird exposed electric contraption that looked like it would electrocute you as soon as you plugged it in. From there, we turned the cylinder by hand to determine if any gears were seized. Apart from the occasional walnut crunching through the gears, the press moved well and everything seemed operational.
We discovered that red squirrels had set up home inside the cylinder. It took several days of vacuuming, scraping and pulling to remove all the nesting materials from the cylinder. Generations of chipmunks had also stashed hundreds of walnuts throughout the press. We swept and vacuumed a lot.
To replicate a print shop of the 1920s-30s era, we envisioned a belt-driven model with a small motor installed on the second floor of the print shop. Our management team agreed to cut a small hole through the ceiling and to add the additional 230-volt circuit required to run a motor in the heritage building. An electrician came in to do the wiring.
In the meantime, the rest of us were busy vacuuming, stripping, cleaning and oiling the press. The distributor table and steel oscillating roller were left uncleaned after its last printing job; this required days of elbow grease. All the rollers were intact but in very bad shape indeed; we sent them to a Toronto company to be re-cast. Due in part to costs (but also because we wanted to continue work and testing), we sent only half the rollers out: one form roller and two distributors. We’ll send the other three in January – at the start of next fiscal.
Testing, troubleshooting.
We tested, observed, puzzled over some of the unknowns. At the beginning, we would turn over the wheel by hand to test mobility and functionality. If gears were stuck, it was usually due to the presence of squirrel-stashed walnuts on the racks. But there were some exciting moments as we made headway.
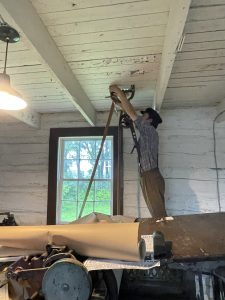
Clay had his hands full calculating pulley dimension and belt tension to regulate the speed of the press. He installed the belt, motor and a clutch lever to engage the belt. He also adjusted the air springs under the press. These function as bumpers against the momentum generated by the weight of the forme and distributing table while working at speed.
Our Pony model came equipped with delivery tapes instead of a fly. While some original tapes were intact, years of use left the tapes were stained and twisted. We bought 40 meters of cotton tape to replace all tapes. We threaded them through the delivery rollers and hand stitched them in place. (In retrospect, we should have laced them in place to ensure a straight seam. As it turns out, the uneven seams cause the tapes to slide off the their spools and travel across the roll. This is definitely on the list of fixes.)
We puzzled over the paper gripper release: how to release them to repack the cylinder? What’s the recommended packing thickness? Where to buy tympan wide enough to fit the Whitlock? So many questions. Thankfully, a member of the Briar Press group stepped up to offer invaluable advice. And with a lot of tinkering, we found the rod that releases the grippers.
Our ‘first edition’ and moving forward
Interspersed with cleaning and restoration, we also set to work on setting type for a first edition. In typical fashion, I bit off more than I could chew by starting work on a newspaper. I’m not sure what I was thinking, but I’ve used almost all available type in the shop to put together a modest first edition of the museum journal. One of our big challenges at the museum is a shortage of spacing material for big projects, but somehow we’ve put together a reasonable facsimile of period-era newspaper.
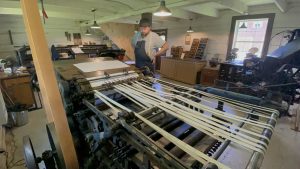
Our short-term plans are to continue to troubleshoot, using a single page forme to figure out details. How to best load the forme on and off the press? How to best orient our papers? We’re still working on levelling the rollers – and until we’ve got all six rollers recovered and on the press, we won’t be able to finalize this work. This also means that we’re working on packing the cylinder appropriately. We also want to correct the installation of the delivery tapes so we avoid slippage. Lastly, we will consider tackling the ink fountain. But as far as I can determine, the fountain is not absolutely necessary for effective printing.
To date, we’ve offered a few public demonstrations of the press in action, much to the fascination of many visitors. Because the Whitlock is a tw0-person press, we are currently limited to demonstrations only a couple times per week, based on our staff availability. On the long term, we’re hoping to offer daily demonstrations of the Whitlock. But to do so also may require that we consider using photopolymer plates or (be still my heart!) possibly restoring our Linotype machine to prepare suitable formes.
It takes a village
While I’m an avid letterpress printer, I’m the first to admit that my mechanical skills are sorely lacking. (See, for example, my post on how to level a platen.) For this reason, I am indeed lucky to be working with a well-rounded and talented staff at the museum. The core team at the museum (Clay, Alex, Bill, myself) were ably assisted by a number of staff members: Bert Potvin, helped with the motor and belt installation; Chris Bedford made the oversize wood furniture and a shipping box for the rollers. Our managers made sure the money and expertise were available when we needed it.
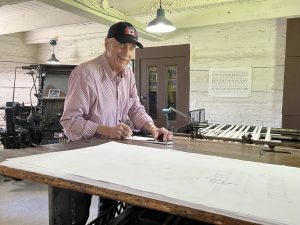
We were also very fortunate to have the assistance and advice of Art Ellis, a volunteer from the Mackenzie Printery and Newspaper Museum in Queenston. He operates the only other working Whitlock press in North America.* Along with colleague Doug Taylor, he made the six-hour drive from southern Ontario to look at the press and offer valuable assistance.
It helped that we did find a couple of manuals for the Babcock and Cottrell two-rev presses. For this I am very grateful to the members of Briar Press. They also recommended Problems of Pressmanship (by Cottrell). If you’re working on a two-revolution cylinder press, this book is a must.
It’s been a fun journey so far — and I’m looking forward to producing some interesting posters and broadsheets on the press. I’ll be sure to share the fruits of our labour. But if you’re into letterpress printing and happen to be in Ottawa, come see for yourself.
Some research sources and pertinent links:
Babcock Optimus Press Manual From Coleman Musem ( OCR Version) (archive.org)
Canadian Printer (canadiana.ca)
Canadian Printer and Publisher (archive.org)
Problems of Pressmanship. New York: C.B. Cottrell & Sons, 1903.
Whitlock Restoration – Videos Playlist. (Youtube)
*Please, please correct me if I’m wrong about other operating Whitlocks! If you do have one that is still functioning or recently restored, please send me a note: sue (at) thecrankypress (dot)ca (remove the spaces). Similarly, if you happen to have a Whitlock operator’s manual or parts list, I’d happily donate my eye teeth to hear from you.
Dear Sue,
My printing partner and I, from the St Lawrence Power and Equipment Museum in Madrid NY, looked at your press a few years ago. We too have a Whitlock pony that we are trying to get going. Ours came from the Commercial Advertiser in Canton NY, as well as 2 Linotypes. We managed to get one Linotype running this year and are starting on the Press. When we visited your museum, the person in the shop knew nothing about the Whitlock and we were disappointed that your press was not in any sort of running order. I know the electrical box you speak of. We photographed it hoping it would give us a clue to something. At that time our press was buried in a barn and we had not gotten it to the Museum.
It looks as you have answered many of the questions that we have. Tipped, Roller sizes, etc. Our cylinder is seized and we are afraid to remove the geared to work on it because we have no info on setting the timing.
Our press was printing a Canton NY newspaper until 1958 when the editor died. The printshop continued as a job shop and printed a 4-H news letter as well as some local collage papers until the shop was bought and closed by a rival printer. We have the chase with the last 4-H newsletter.
Anyway, we have to talk. My number is —-. My partner in this is Bob O’Marah. He is 90 and was a printer his entire working life. Newspapers. Watertown Daily Times, Ogdensburg Journal, Oneida Press Republican, and others. I look forward to hearing from you.
Ted Ritzko
Hi Ted,
Delighted to hear you’re working on the Whitlock. I’ve sent you an email to follow up. All best, Sue
I have a whitlock printing press also . Plus several flong
I’d love to hear more about your Whitlock!